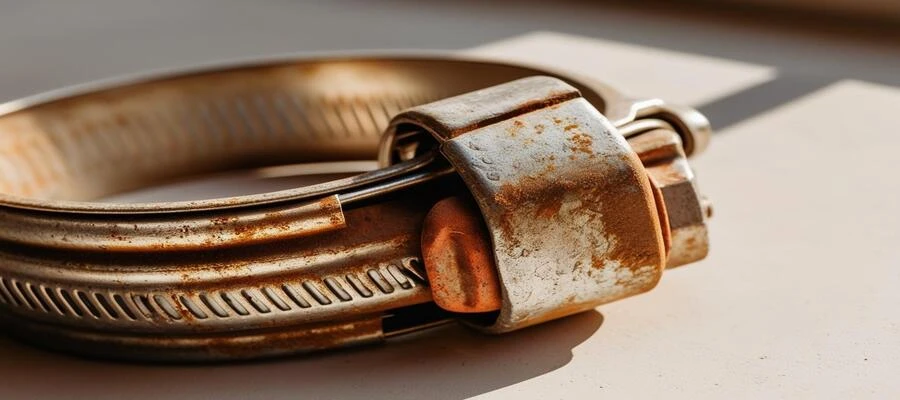
Hose clamps are crucial components in various applications, and recognizing when to replace them is essential for maintaining system integrity. Here are five signs that indicate it's time for a replacement: first, visible corrosion or rust on the clamps; second, leaking fluids around the connection; third, loss of tightness or loose clamps; fourth, cracked or damaged hose material near the clamps; and fifth, frequent adjustments or repairs needed. Addressing these signs promptly can prevent further damage and ensure reliable performance.
The Importance of Maintaining Hose Clamps
Maintaining hose clamps is vital for the overall performance of any system they are part of. Properly functioning clamps ensure that hoses remain secured, preventing leaks and system failures. Regular inspection and maintenance help identify wear and tear, allowing for timely replacements before issues arise. This not only prolongs the life of the hoses but also enhances safety by reducing the risk of accidents caused by leaking fluids. Investing time in maintenance can lead to significant savings by avoiding costly repairs and downtime.
Common Risks of Ignoring Worn-Out Hose Clamps
Ignoring worn-out hose clamps can lead to several serious risks that affect both safety and functionality. These risks include:
- Fluid Leaks: Can cause contamination and operational failures.
- Increased Downtime: Replacing damaged components takes time and resources.
- System Failures: May lead to costly repairs and replacements of larger systems.
- Safety Hazards: Leaking fluids can create dangerous working environments.
- Hose Damage: Worn clamps can damage hoses, leading to additional replacements.
Being proactive about clamp maintenance prevents these potentially severe consequences.
Sign 1: Visible Corrosion or Rust on the Clamps
Visible corrosion or rust on hose clamps is a clear indication that they need to be replaced. This deterioration weakens the clamp's structure and reduces its ability to hold hoses securely. Corroded hose clamps can lead to leaks, compromising the entire system. It’s important to address any signs of rust promptly, as they can escalate into more significant problems. Regular inspections can help catch corrosion early, allowing for replacements before they cause damage. Utilizing stainless steel or coated clamps can mitigate corrosion risks.
How Corrosion Affects Clamp Performance
Corrosion significantly affects the performance of hose clamps by weakening their grip and structural integrity. As clamps corrode, they lose their tightness, which can result in fluid leaks and increased pressure on the hoses. This diminished performance may cause clamps to fail unexpectedly, leading to system malfunctions. In addition, the uneven surfaces created by corrosion can cause additional wear on the hoses, resulting in premature damage. Ensuring that hose clamps are free from corrosion is essential for maintaining a secure and reliable connection.
Preventing Rust on Hose Clamps
Preventing rust on hose clamps is essential for ensuring their longevity and performance. Here are some effective strategies:
- Use Stainless Steel Clamps: These are more resistant to corrosion.
- Apply Anti-Rust Coatings: Protective layers can significantly reduce rust formation.
- Regularly Inspect and Clean Clamps: Removing dirt and moisture helps prevent oxidation.
- Ensure Proper Installation: Tighten clamps correctly to avoid water traps that cause rust.
- Store Clamps Properly: Keep them in a dry place to prevent environmental damage.
Implementing these measures can greatly enhance the durability of hose clamps.
Sign 2: Leaking Fluids Around the Connection
Leaking fluids around the connection is a significant sign that hose clamps need replacement. This leak often indicates that the clamp is no longer tight or secure, which can be due to wear, corrosion, or improper installation. Addressing fluid leaks promptly is crucial, as they can lead to larger system issues, wastage of resources, and safety hazards. Regular checks for leaks can help identify clamp failures early, allowing for timely replacements to maintain system efficiency and safety. Don’t overlook leaks, as they signal potential problems.
Why Leaks Indicate Clamp Failure
Leaks around hose connections are a clear indication of clamp failure, often resulting from several factors. First, corrosion or rust can weaken the clamp, reducing its ability to maintain tightness. Second, if the clamp becomes loose due to vibration or temperature changes, it can no longer provide a secure hold, leading to leaks. Finally, worn-out clamps may not fit properly, creating gaps that allow fluids to escape. Ignoring these leaks can result in significant damage to the system and increase maintenance costs.
Sign 3: Loss of Tightness or Loose Clamps
A loss of tightness or loose clamps is a critical sign that replacement is necessary. Loose hose clamps can lead to serious issues, including fluid leaks, hose damage, and even system failures. It’s essential to regularly check clamps for tightness, as even slight looseness can compromise the integrity of the entire system. Factors like vibration, temperature fluctuations, and corrosion can cause clamps to become loose over time. Addressing this sign promptly can prevent further damage and ensure that your system operates smoothly.
The Dangers of Loose Hose Clamps
Loose hose clamps pose several dangers that can affect both safety and system functionality. Some of the key dangers include:
- Fluid Leaks: Can lead to contamination and operational failures.
- Hose Damage: Increased friction and movement can tear or weaken hoses.
- System Failures: May result in costly repairs or replacements of critical components.
- Safety Hazards: Leaking fluids can create dangerous conditions for workers.
- Increased Maintenance Costs: Frequent repairs due to clamp failure can add up.
Maintaining proper tightness in hose clamps is crucial to preventing these risks.
How to Properly Tighten Hose Clamps
Properly tightening hose clamps is essential to ensure a secure connection and prevent leaks. Follow these steps for effective tightening:
- Choose the Right Tool: Use a screwdriver or socket wrench appropriate for the clamp type.
- Align the Hose Correctly: Ensure the hose is properly positioned before tightening.
- Tighten Evenly: Apply consistent pressure to avoid damaging the hose or clamp.
- Do Not Over-Tighten: This can cause hose compression and eventual damage.
- Check Tightness Regularly: Keep an eye on clamps to maintain proper tension.
By following these steps, you can ensure that hose clamps remain tight and secure.
Sign 4: Cracked or Damaged Hose Material Near the Clamps
Cracked or damaged hose material near the clamps is a troubling sign that indicates the need for replacement. This damage often occurs when clamps are too tight, causing unnecessary pressure on the hose, or when worn clamps allow excessive movement. Addressing hose damage is crucial, as it can lead to leaks and system failures if left unattended. Regular inspections of both hoses and clamps can help prevent this issue, ensuring that connections remain secure without compromising the hose integrity. Replace damaged hoses promptly to maintain functionality.
How Clamps Can Damage Hoses Over Time
Hose clamps can damage hoses over time due to several factors. First, if clamps are over-tightened, they can create pressure points that lead to cracks and tears in the hose material. Second, corroded or worn clamps can cause uneven wear, resulting in weak spots along the hose. Finally, loose clamps can allow excessive movement, leading to abrasions and premature hose failure. It’s essential to monitor both clamps and hoses to prevent damage and ensure a reliable, leak-free connection between components.
Choosing the Right Clamp to Prevent Damage
Choosing the right clamp is essential to prevent damage to hoses. Here are key considerations:
- Clamp Size: Ensure the clamp is the correct size for the hose to provide a secure fit.
- Material: Select corrosion-resistant materials, such as stainless steel, for durability.
- Type of Clamp: Choose a clamp type that suits your application (e.g., worm gear, spring).
- Tightening Mechanism: Opt for a mechanism that allows even tightening without excessive force.
- Application Specifics: Consider the pressures and temperatures involved in your system.
Selecting the appropriate clamp helps maintain hose integrity and prevents premature damage.
Sign 5: Frequent Adjustments or Repairs Are Needed
If you find yourself making frequent adjustments or repairs to hose clamps, it’s time for a replacement. Constantly loose clamps or recurring issues indicate that the current clamps are worn out or unsuitable for the application. This situation can lead to increased downtime and frustration, as well as potential damage to hoses and the surrounding system. Upgrading to more durable and reliable clamps can reduce the need for frequent adjustments, ensuring a stable and secure connection. Invest in quality clamps to enhance system reliability and performance.
Upgrading to Durable and Reliable Clamps
Upgrading to durable and reliable hose clamps is essential for reducing maintenance efforts and enhancing system performance. When selecting new clamps, consider factors such as material strength, corrosion resistance, and the specific application requirements. Stainless steel clamps offer superior durability and resistance to environmental factors. Additionally, ensure the new clamps provide a proper fit and effective tightening mechanisms to prevent future issues. This upgrade will not only save time on repairs but also ensure a safer, more efficient operating environment.
How to Choose the Right Replacement Hose Clamps?
Choosing the right replacement hose clamps involves several important considerations. First, determine the appropriate size for the clamps, ensuring they match the diameter of the hoses. Second, select the material based on the environmental conditions and potential corrosion risks; stainless steel is often a great choice. Third, understand the specific application requirements to choose the right clamp type, whether it’s adjustable or fixed. Finally, consider the tightening mechanism to ensure ease of use and safety during installation. These factors will ensure you select suitable replacement clamps.
Key Factors to Consider When Replacing Clamps
When replacing hose clamps, several key factors should be considered to ensure the right choice:
- Size: Measure the hose diameter to select the appropriate clamp size.
- Material: Choose a material that offers durability and resistance to corrosion.
- Type: Select the clamp type that best suits your application and requirements.
- Tightening System: Ensure the system allows for easy installation and secure tightening.
- Application Conditions: Consider temperature and pressure requirements for your specific use.
Taking these factors into account will help you make an informed decision when replacing hose clamps.
When to Seek Professional Help for Clamp Replacement
Knowing when to seek professional help for hose clamp replacement is crucial. If you encounter persistent issues such as severe leaks, extensive hose damage, or difficulty in tightening clamps, it’s time to consult a professional. Additionally, if the application involves high pressures or critical systems, expert assistance ensures that replacements are done safely and effectively. Professionals can provide guidance on the right clamp types and sizes, preventing mistakes that could lead to future failures. Don’t hesitate to ask for help when needed.