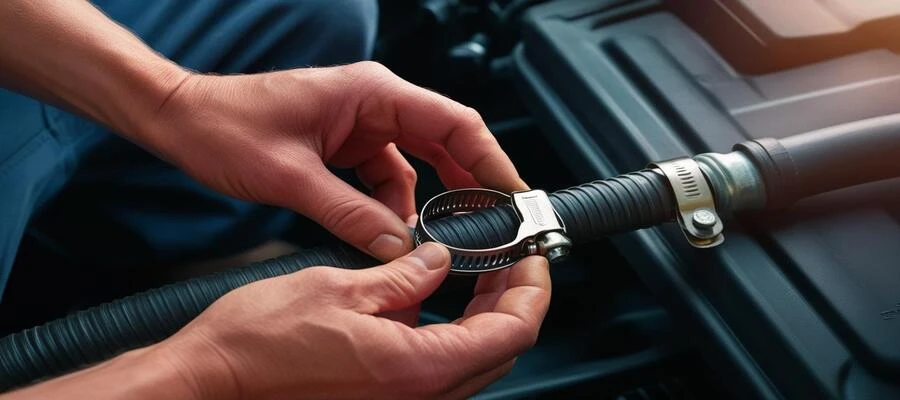
Hose clamps are essential components used to secure hoses in various applications. However, improper assembly can lead to significant issues, such as leaks or failures. Understanding the common mistakes and the correct practices in hose clamp assembly is crucial for ensuring a reliable connection. This article will outline the importance of proper hose clamp installation, the typical errors made, and the best practices to follow for effective and durable assembly.
Why Proper Hose Clamp Assembly Is Crucial
Proper hose clamp assembly is crucial for several reasons. Firstly, it ensures a secure connection between the hose and its fitting, preventing leaks that could lead to fluid loss or damage. Secondly, correct assembly contributes to the overall safety of the system; loose or improperly fitted hoses can cause catastrophic failures. Lastly, investing time in proper installation improves the longevity of the hoses and clamps, saving money on replacements and repairs in the long run.
Consequences of Improper Hose Clamp Installation
Improper hose clamp installation can result in serious consequences. The most immediate issue is leakage, which can cause fluid loss and create hazardous environments. In mechanical systems, such leaks may lead to decreased performance or damage to other components. Moreover, an incorrectly installed hose clamp can fail dramatically, risking safety and leading to costly repairs. Therefore, understanding and avoiding installation mistakes is essential for maintaining system integrity and ensuring operational safety.
Common Mistakes in Hose Clamp Assembly
To ensure effective hose clamp assembly, it is vital to be aware of common mistakes:
- Using the Wrong Size Hose Clamp: A clamp that is too large or too small cannot provide a secure fit.
- Over-Tightening or Under-Tightening: Incorrect tightening can damage the hose or lead to leaks.
- Misaligning the Hose Clamp: Proper alignment on the connection point is essential for a good seal.
Bu hatalardan kaçınmak, güvenilir ve etkili bir montaj sağlamak için kritik öneme sahiptir.
Using the Wrong Size Hose Clamp
Using the wrong size hose clamp is a frequent mistake that can compromise the integrity of the assembly. A hose clamp that is too small may not fit around the hose, leading to excessive pressure and potential rupture. Conversely, an oversized clamp will fail to provide the necessary grip, allowing the hose to slip and leak. To avoid this error, always measure the hose diameter and select a clamp designed for the specific size range.
Over-Tightening or Under-Tightening Hose Clamps
Over-tightening or under-tightening hose clamps are critical errors that can lead to failure. Over-tightening can cause damage to the hose, compromising its structure and leading to leaks. On the other hand, under-tightening may result in inadequate sealing, allowing fluids to escape. To achieve the correct tightness, it is essential to follow the manufacturer’s guidelines and use a torque wrench if possible. This ensures the clamp is secured properly, balancing pressure and hose integrity.
Misaligning the Hose Clamp on the Connection Point
Misaligning the hose clamp on the connection point is another common mistake. Proper alignment is crucial for creating a tight seal between the hose and fitting. If the clamp is misaligned, it can lead to uneven pressure distribution, increasing the risk of leaks. To ensure correct alignment, position the hose so that it sits evenly on the connection point before applying the clamp. Carefully adjust the clamp during tightening to maintain proper alignment throughout the process.
Correct Practices for Effective Hose Clamp Installation
For an effective hose clamp installation, the following correct practices should be observed:
- Selecting the Right Size Hose Clamp: Ensure the clamp fits the hose diameter appropriately.
- Achieving Proper Tightness: Follow torque specifications to secure the clamp adequately.
- Aligning the Clamp Correctly: Position the clamp for even pressure distribution on the connection.
Bu uygulamalar, güvenilir bağlantılar oluşturarak sistemlerin performansını artırır.
Selecting the Right Size Hose Clamp for a Secure Fit
Choosing the right size hose clamp is essential for a secure fit. To do this, measure the outer diameter of the hose where the clamp will be placed. Consider the hose's flexibility; it may change shape under pressure or during operation. Select a clamp that offers a range slightly above the measured size to accommodate any variations. This ensures the clamp can grip the hose tightly, preventing leaks and ensuring durability in the connection.
Achieving the Proper Tightness for Hose Clamps
To achieve proper tightness for hose clamps, it is crucial to follow systematic guidelines. Begin by placing the clamp around the hose and adjusting it to the desired position. Use a screwdriver or wrench to tighten the clamp gradually, ensuring even pressure. Refer to the manufacturer’s recommended torque specifications; if unavailable, aim for a snug fit that compresses the hose slightly without causing distortion. Regularly checking tightness can improve reliability, especially in dynamic systems.
Best Materials for Hose Clamp Durability
Hose clamp durability largely depends on the materials used in their construction. Stainless steel is one of the best options due to its corrosion resistance and strength, making it suitable for various environments, including those with exposure to moisture and chemicals. Galvanized steel is another good choice, offering decent corrosion resistance at a lower cost. For high-temperature applications, clamps made from specially coated materials or brass can provide enhanced performance and longevity.
Tools You Need for Proper Hose Clamp Assembly
Having the right tools is essential for proper hose clamp assembly. Basic tools include a screwdriver and pliers, which assist in adjusting and tightening clamps. A torque wrench is highly recommended to ensure accurate tightening and prevent over or under-tightening. Additionally, a hose cutter can help achieve clean, straight edges for better sealing. Finally, a measuring tape is crucial for selecting the correct clamp size, making the assembly process more efficient and effective.
How to Inspect and Maintain Hose Clamps
Regular inspection and maintenance of hose clamps are vital for ensuring their functionality. To inspect, visually check for signs of wear, corrosion, or misalignment. Ensure that the clamp is tight and positioned correctly. Maintenance involves cleaning the clamps, especially in dirty or corrosive environments, to prevent buildup that can mask defects. Lubricating moving parts can enhance performance. If any damage is noted, replace the hose clamp promptly to maintain system integrity.
Signs of Wear and Damage in Hose Clamps
There are several signs of wear and damage to look for in hose clamps. These include visible rust or corrosion, which compromises the clamp’s strength. Cracks or deformities in the metal indicate that the clamp has been over-tightened or exposed to excessive stress. Additionally, a loose clamp that shows movement around the hose connection is a warning sign. Regular monitoring of these signs helps ensure early detection of issues, promoting safe and reliable operations.
When and How to Replace Faulty Hose Clamps
Faulty hose clamps should be replaced immediately to prevent system failures. If signs of wear or damage are observed, remove the clamp for inspection. If it is indeed faulty, choose a suitable replacement that meets the same size and material specifications. To replace, first clean the hose and connection point, then install the new clamp following correct assembly practices. Tighten the clamp appropriately and check alignment to ensure a secure and effective fit.